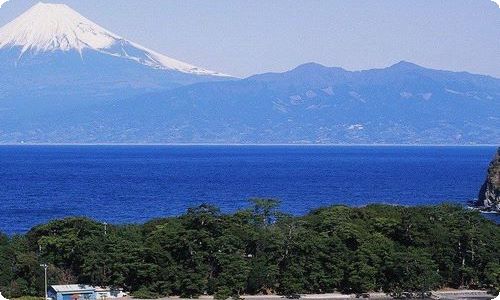
我为降本增效献一计
我为降本增效献一计,降低成本一直以来就是企业在管理中非常重视的内容,但是想要降低成本是一件很难的事情,需要经过多方面的实验,下面小编带大家简单了解一下我为降本增效献一计.
我为降本增效献一计1
北京凌云东园公司黄骅工厂路华:在降本提质增效实施过程中,应该深入一线从一点一滴做起,在实践中探索和创新,就凌云黄骅工厂来说,考虑到辊压外板产品在生产过程中由外板底部定位,可将外板产品头部缩短10MM,经过对10种辊压产品进行试验,均不影响产品结构及产品质量,可直接节约原材料。
北京凌云东园公司重庆工厂质量部 张硕:通过产品组装搭接间隙的最小化管理,并对外协件产品焊接的实间隙值精化下公差管理,加密对焊接过程的管控,从而全面降低产品补焊率,降低质量损失。
北京凌云东园公司黄骅工厂物流部 许伟:在降本提质增效实施过程中注重从实际出发,基于当前产量较预期下降的实际情况,经过和物流公司协商,对每月不满正常工作日生产情况下固定仓储服务费改为按天结算,可有效降低仓储费用。
北京凌云东园公司重庆工厂生产部 李伟强:重点焊接工序安装在线电流监测器,通过可视化管理,加强对产品焊接质量的控制,可有效提升焊接质量稳定性,减少返工成本。
北京世东凌云公司运营管理部生产经理 周同:在降本提质增效实施过程中,注重创新发展,提升工艺水平,根据产品结构、工艺要求,自主设计半自动涂胶设备、自动冲压机设备,降低人工成本,提高生产效率。改进工艺设备,面对产品日趋多样化的现状,改进贴膜机下端刮板,可试用于多种车型形态。优化生产布局, 消除浪费,提升合理工位占用,提高生产线效率。
北京世东凌云公司运营管理部生产科长 安石、顺义分公司生产科长 王金东: 在降本提质增效实施过程中,坚持开拓高性能、高附加值产品,实现PP+TPV挤出工艺突破。借鉴韩国现有生产线模式,引进其较为成熟的PP+TPV新材料及膜内贴绒生产工艺,更好的实现产品轻量化,同比PVC I/S产品,在同等长度的前提下重量减少34%。新材料新工艺技术的成功引入,既满足了客户需求,又降低了制造成本,同时制造成本的降低为后续新车型产品的竞价提供了优势。
北京世东凌云公司开发部科长 丁兴豪: 在降本提质增效实施过程中,对于某新开发模具,通过研讨、试验发现,只需变更旧模具中一个模腔,即可实现新产品模具开发要求。旧模具修改费用预计3万元左右,直接实现降本约10万元。
凌云股份制造分公司质量部 张雯:通过QC项目可解决某车型门槛件长期存在的工装废料反弹问题,大幅度的提高了产品外观质量,减少内部废品损失和外部返修费用。
凌云股份制造分公司质量部宗绍辉:通过调整设备动作顺序消除奔驰单元某非标冲5序侧冲孔孔偏不良问题,降低了废品损失,同时还提高了设备冲孔精度。
我为降本增效献一计2
炼铁厂#号高炉全体职工,面对严峻的市场形势,已做好长期应对困难的准备。 #号高炉要求每个班组长和党员带头制定”勤俭节约,从我做起”的承诺,积极响应公司和炼铁厂倡导的“勤俭节约、节能降耗”的号召。坚持节约,反对浪费,从我做起,从点滴做起,从力所能及的事情做起。
号高炉从优化工艺、优化操作、加强设备的维护保养、杜绝跑冒滴漏、修旧利废,降低机物料消耗、安全生产等方面着手,发挥全员参与的优势,用实际行动推进降本增效的`实现。
开展科技创新,改善生产及成本指标
针对炼铁的工艺特点,实施“三优化”措施:优化炉料结构、优化操作制度和优化设备运行。
优化炉料结构
在不影响炉况顺行和产量、质量的情况下,配加大比例生矿,逐步降低球团的配加比例,达到降成本的目的。从2009年5月-8月的高炉配加大比例生矿生产实践的跟踪分析来看,认为将生矿比例控制在10%-20%,球团比例控制在0-5%,吨铁成本下降20-30元,单座高炉全年成本降低500万至1000万,降成本效果显著。
优化操作制度
高炉顺行稳定是降本增效的重要因素。摸索适宜#号高炉上部装料制度及下部送风制度,使上下部调剂相适应,提高煤气利用率,保持充沛的渣铁物理热,保持稳定的中心气流和边缘气流,使高炉稳定顺行,为降低生铁含硅,提高煤比及降低焦比奠定基础。根据#号高炉炉型特点,认为矿批在10t-12t左右的大矿批分装是适合#号高炉的装料制度,对降本增效意义重大。
优化设备运行
减少高炉设备故障率是降低成本的重要方面。认为机修辅助车间搞好高炉设备点检,是保证高炉设备正常运转的关键。
坚持“一执行、一提高、一降低”重点节能降耗举措,即坚持执行低硅铁冶炼、提高煤比和降低焦比。
降低生铁含硅量,提高煤比,降低焦比。
炼铁工序能耗占整个钢铁工序的60-70%,工序成本也占整个钢铁系统成本的50-55%,钢铁企业是否有效益、竞争力,关键看炼铁成本的高低,而提高喷煤比、降低焦比则是降低炼铁成本的重中之重。今年#号高炉平均入炉焦比徘徊在420kg/t上下,平均生铁含硅在0.60%左右。虽然这一指标与炉型不合理、焦炭质量不理想、入炉品位偏低有直接关系,但这并不是唯一的原因。因此,#号高炉要有所突破,除了持续降低焦比和生铁含硅量之外,稳定控制、避免反复,对生产、降耗意义重大。
脱硫。由于原燃料成分、质量的不稳定,小高炉控制生铁含硫在较窄范围在一定程度上带动了成本上升,建议科学把握质量要求与成本控制的平衡点;
狠抓基础管理,确保高炉安全生产
将8S作为管理重心,真抓实干。
一个企业管理的成熟与否,直接可以影响生产成本,向管理要效益是个很实在的想法,面对越来越严重的外部竞争,也只有加强管理才能降低成本。从许多大型优秀企业(海尔公司就是最好的例证)的反馈效果来看,8S是降低管理成本的最有效和最直接的办法。8S很简单,班组长和工人都容易掌握,核心的问题就是打扫卫生,清理清理再清理。有人说很简单,其实不简单,长期坚持下去就会更难。8S管理真正做到了,做好了,是基础管理的极大进步。
建立降本增效长效管理机制。
按管理层次,将降本增效指标层层分解落实到车间级、班组级、作业区级,奖罚分明。
建立长期有效的安全培训机制。
定期召开提高员工素养和安全、操作水平的培训课,提高职工队伍的整体素质,形成学技术、钻业务的好风气。让每一个员工从自觉开始,变“要我安全”为“我要安全”。
建立合理的劳动竞赛管理机制。
开展劳动竞赛,制定合理的质量及产量目标,并且分解到班组和个人,将效益和工作挂钩,激发职工的荣誉感和紧迫感。但是需要做大量的统计分析工作,建立比较可行的考核基准才行。建议在炉内操作上,把炉温、含硫、料批,产量、焦比、质量等操作指标分解到每个班组,班与班之间开展竞争,加强三班统一操作,严格控制炉温及渣碱度,确保高炉稳产高产。在炉外操作上,重点把正点出铁、铁量差、铁口角度合格率,设备维护等操作指标作为竞赛的主要内容,班组与班组比,岗位与岗位比,个人与个人比,加强生产设备的动态管理,减少各类事故,为炉内操作创造有利条件。
小技改也能解决大问题。
全员行动,小改造,大收益。管理创新同技术创新相结合,积极开展“小改小革”活动,进行设备局部改造或工艺优化